POLYSTY High Impact Polystyrene
Technology for two different HIPS processes:
HIPS for Virtually All Markets
-
Demonstrated commercial technology
- Specialty ATP grades
- Standard extrusion and injection grades
- Small capital investment
- Low cost operation and maintenance
- Good rubber efficiency
- High consistency and reproducability
- Under 150 ppm of residual styrene monomer
- Near-zero emissions
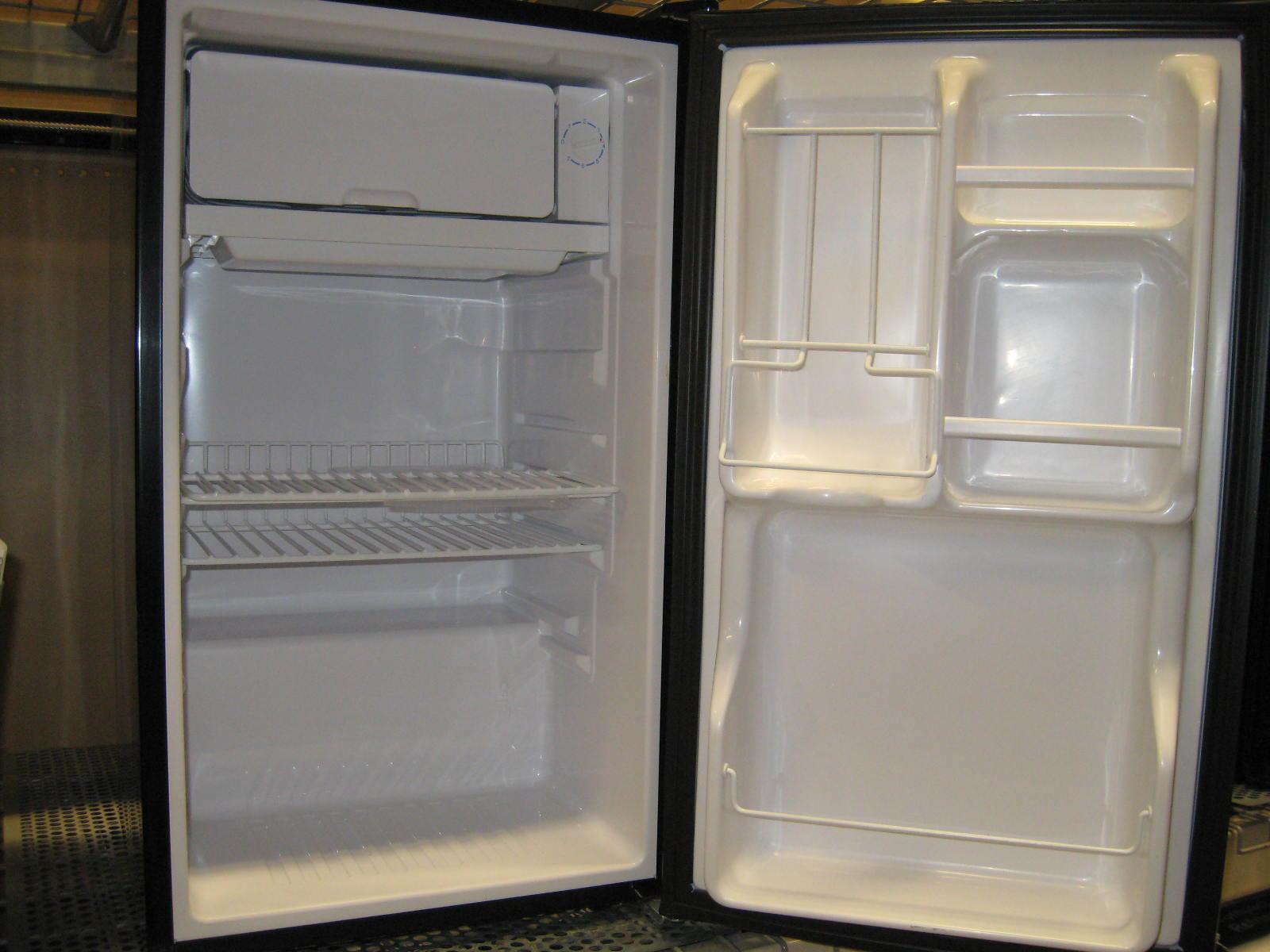
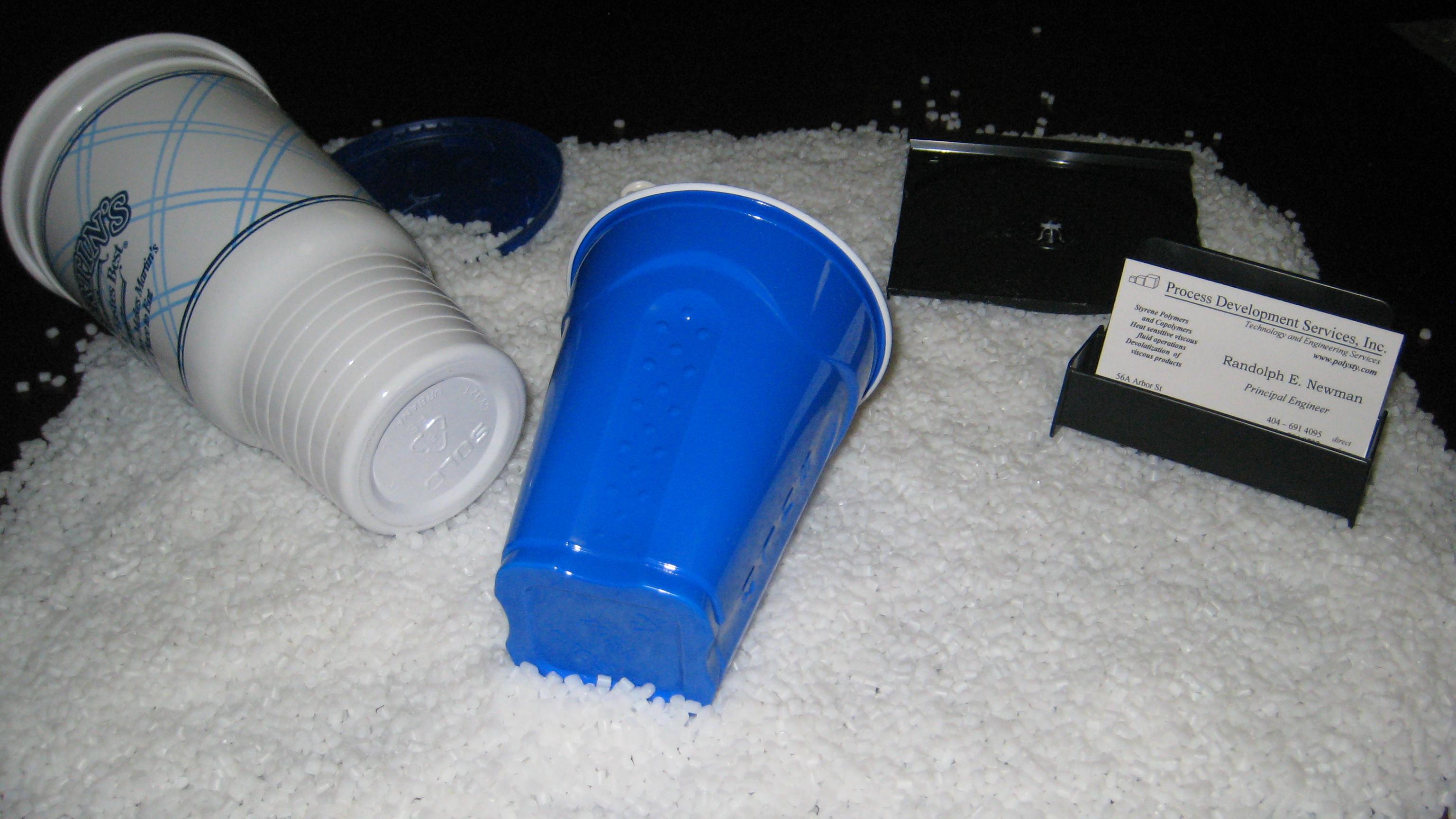
Product Capability – ATP Specialty HIPS
POLYSTY Agitated Tower Process (ATP Technology) inverts the polybutadiene rubber phase with true phase inversion by virtue of its proven plug flow profile. The result is rubber efficiency that is usually 30% better (or more) than most competitive HIPS. ATP Specialty products may be used to make Super High Impact PS (SHIPS), high gloss products, refrigerator liners and other refrigerator interior parts, base for FR compounding, and other application usually reserved for ABS.
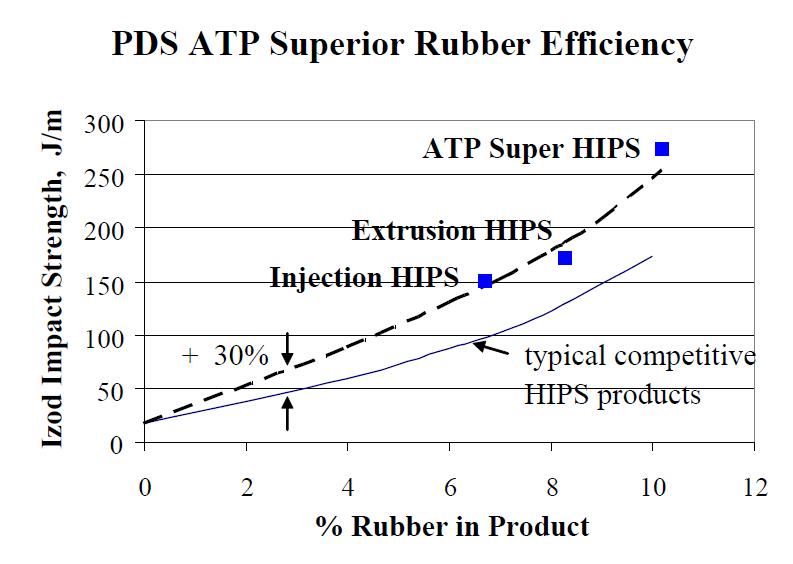
Product Capability – Swing Line HIPS
POLYSTY Swing Line Technology makes HIPS to satisfy 90% of market needs, with minimal capital investment. Typical products from swing line HIPS are extruded sheet for high speed thermoforming, refrigerator trays, food packaging, toys, household items, personal care items, thin and thick wall injection molding, toy parts, copolymer blending, etc.
Swing Line Technology allows the producer to make a full slate of GPPS products in the same line, to meet local market needs and seasonal demand. Thus, small markets can be fully satisfied with minimal investment in a single production line.
Capital Investment
POLYSTY ATP Technology investment is comparable to other plug-flow and semi- plug flow technology.
POLYSTY Swing Line Technology may be installed at a lower investment than any other HIPS technology.
All POLYSTY technology design is engineered to make the best use of third-party equipment packages. We optimize our designs to fit third-party equipment capacities, such as pumps, rubber dissolving equipment, pelletizing, etc. We also design a prudent amount of over-capacity for different packages to allow for transient process conditions, based on our years of production experience. Therefore capital requirement is optimized for minimum investment per unit of reliable production.
Typical HIPS production can be installed economically from 20,000 to 100,000 metric tons per year in a single line. Capital investment figures are available upon request and depend on licensee scope.
Operation and Maintenance
POLYSTY HIPS process design is engineered for low utility costs. For example, cooling tower water and refrigerated coolant are used according to the location and cost structure of the site. Heat of reaction is also recovered where practical. Other proprietary steps are also practiced.
POLYSTY Technology also allows minimal numbers of operating personnel.
The technology is demonstrated in commercial plants, and uses only proven third-party equipment packages. This design philosophy results in a plant that greatly improves operational simplicity and stability, while reducing installation costs, operating costs, and maintenance costs.
Product and Process Control
POLYSTY Technology is designed to be as fully automated as possible, which eliminates shift and operator variability. The control system assures consistent and successful rubber dissolving.
The engineered system design enables a high degree of product reproducibility, day-to-day, season-to-season, and year- to-year. Most owners achieve 6-sigma production.
Safety and Environmental
We use design features and equipment throughout the process to meet modern international safety and environmental standards.
The DIERS method is used for all styrene-containing vessels. Reactors are designed to contain runaway reactions in case of power loss, preventing environmental discharge and allowing faster re-starts.
All process systems are designed to prevent spills, leaks, and point- source emissions without excessive maintenance. We specify demonstrated technology to prevent, or minimize, point-source emissions from hydrocarbon pumps, vessel agitators, and vessel flanges and fittings.
We will be happy to supply more information.
Please contact POLYSTY