C-Star Plus GPPS
World Class GP Polystyrene
with Profitable Economics
- Wide range of highly competitive crystal-clear Polystyrene products
- Low capital investment
- Simple, safe operation
- Low-cost operation and maintainence
- Consistent and reproducible products
- Under 150 ppm of residual styrene
- Rapid product transitions
- Near-zero emissions
- No solvent addition
- ideal low-cost GPPS melt for for Continuous EPS
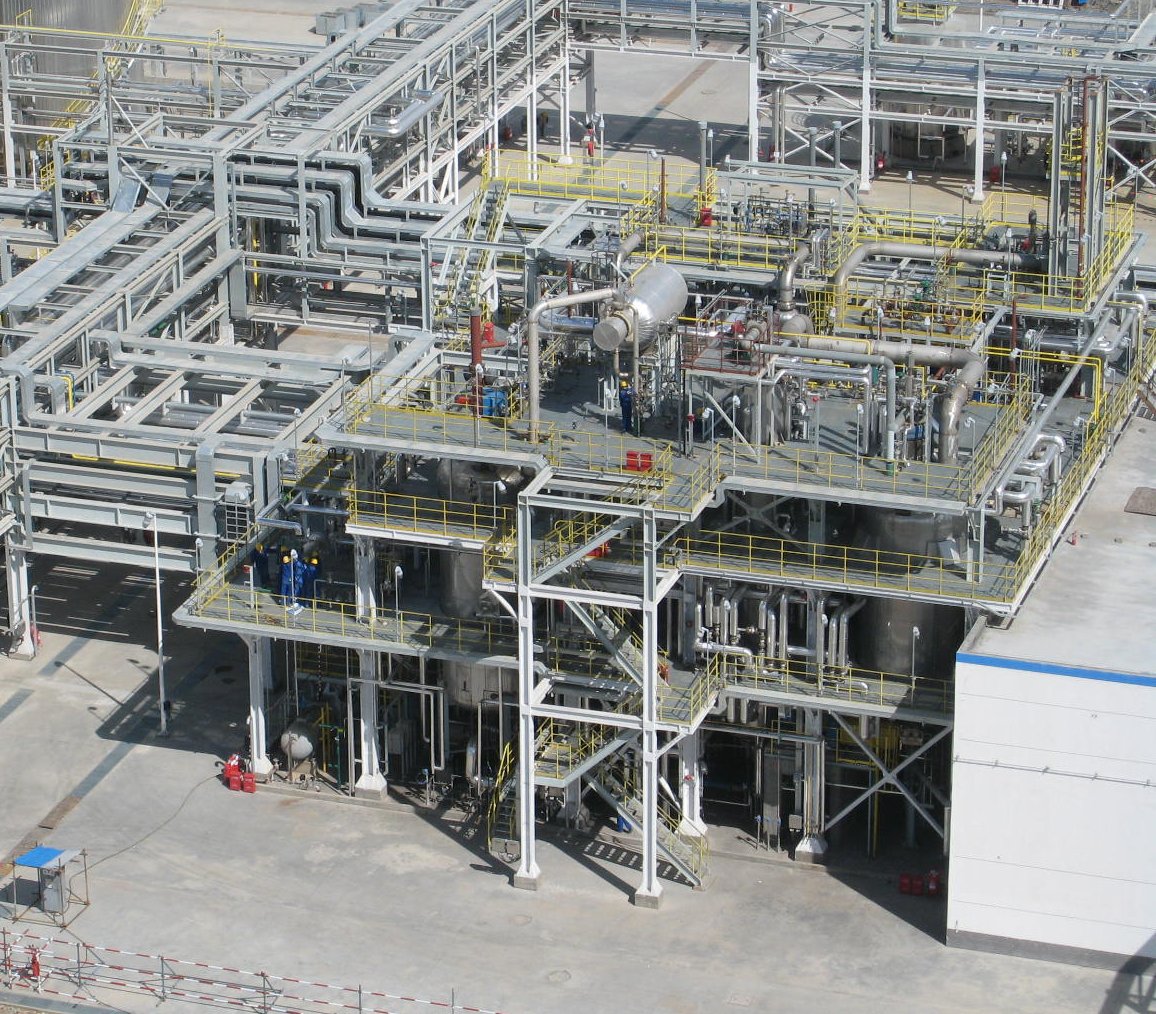
90,000 tonne C-Star Plus unit
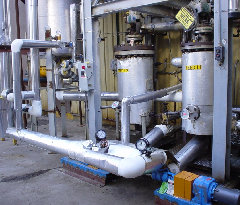
POLYSTY semi-works pilot line
Product Capabilities
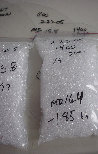
sample GPPS product
C-Star Plus is capable of producing virtually any competitive crystal Polystyrene grade. Melt index may range from as low as 1.6 to above 20. Vicat softening temperature values can range from 90° to 108°C
Process Design may be tailored to meet local market requirements.
All GPPS products can be produced at less than 150 ppm residual styrene with the POLYSTY DV-Plus devolatization process module.
C-Star Plus is an ideal low-cost solution to make GPPS melt as feedstock to a continuous pentane addition EPS process unit.
Capital Investment
C-Star Plus may be economically installed in any capacity from 20,000 to 130,000 metric tonnes per year. Typical ISBL (Inside Battery Limits) installed cost ranges from $ US 150-250 / tonne, depending on size and the options that are chosen by the client.
Operation and Maintenance
C-Star Plus uses fewer pieces of equipment than competitors, which greatly improves operational simplicity and stability, while reducing installation costs, operating costs, and maintenance costs.
The process is designed to achieve rapid transitions between product grades, for higher on-specification production results.
With fewer pieces of equipment and high degree of automatic control, there are fewer process variables to drift, and lower probability of operator error. C-Star Plus design enables the owner to achieve 6-sigma production.
Safety and Environment
We use design features and equipment throughout the process to meet and exceed modern international safety and environmental standards.
The DIERS method is used for all styrene-containing vessels. Reactors are designed to contain runaway reactions in case of power loss, preventing environmental discharge and allowing faster re-starts.
All hot oil systems are designed to prevent spills and leaks. As with the vessels, we specify oil pumps, valves, flanges, and fittings to intrinsically prevent leaks and point-source emissions without excessive maintenance.
For monomer containment, we specify demonstrated technology to prevent, or minimize, point-source emissions from monomer and polymer pumps, vessel agitators, and vessel flanges and fittings.
Process Description
C-Star Plus acheives its low capital and operating costs, reliability, and easy operation from simplicity of design and choice of well-demonstrated equipment.
A single main reactor with specially designed internal components is used, followed by the POLYSTY' proprietary Finisher Reactor. DV-Plus is used to remove volatile impurities to very low levels.
POLYSTY service to you may range from
low-cost design modifications to improve profits from existing faculties
to supply of key equipment,
to design, engineering, procurement, and turnkey construction/commissioning/startup.
We will be happy to supply more information.
Please contact POLYSTY